At Zimmer and Peacock we manufacture electrodes, which upon the addition of polymer, enzymes, antibodies, RNA, DNA, aptamers, ionophores etc become biosensors. sensors and medical diagnostics.
We have a division in our products and services which is based on whether the electrodes are intended for research and the research community or whether the sensors are for product development and are going into a finished product in the medium term.
The questions we are often asked is '...how do you ensure your electrodes are repeatable/suitable for my application/product...'. The short answer is that if the sensors are on our website and sold via the webstore etc then we visually inspect them. In this note we discuss how we guarantee electrodes that are intended for product development and manufactured products by sampling and appropriately electrochemically functionally testing them.
ELECTRODES INTENDED FOR PRODUCT DEVELOPMENT AND MANUFACTURED PRODUCTS
If the sensors/electrodes are intended for a development programme or a manufactured product, where repeatability etc is important then we functional test samples from the batch and ensure their functional performance is within agreed limits.
The functional QA testing is done for each customer for a fundamental electrochemical reason, and the reason is that the way we test a sensor for a customer has to reflect the way the electrode will be finally be used by their final customers.
There are so many ways a final electrochemical assay will be run on a biosensor and medical diagnostic product including: cyclic voltammetry, differential pulse voltammetry, square wave voltammetry, pulse voltammetry, electrochemical impedance spectroscopy, amperometry, single frequency analysis, etc. ZP are an experienced industrial electrochemists, and we know that if we test all our electrodes for a customer/client by cyclic voltammetry but their assay is in fact amperometry then the testing in the factory is not close enough to the real-world-use-case to truly say that what is shipped from our loading bay has the performance to work in your product. For example if your assay is amperometry as -100 mV vs reference then we need to test samples from the batch sensor/electrode at -100 mV vs. reference, if you're assay is single or multiple frequency analysis then we need to test at those frequencies.
To have repeatable and stable medical diagnostic product there needs to be a close partnership in place between the supplier of the electrodes and the partner some basic parts need to be in place.
- A mutual NDA/CDA in place so we can have a technical conversation.
- An understanding from ZP's side as to how the electrodes will be used.
- ZP proposes a factory tests, including an electrochemical assay with a PASS/FAIL criteria.
- ZP ships electrodes/batches in accordance with a PASS in the factory testing.
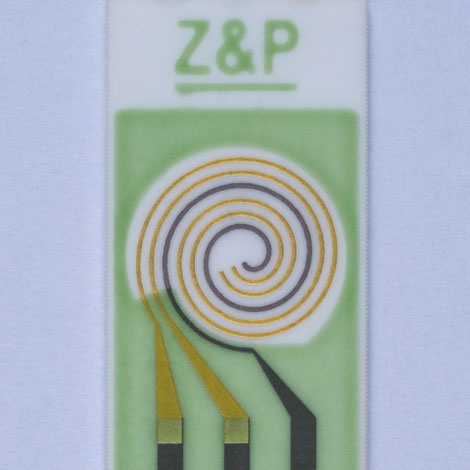
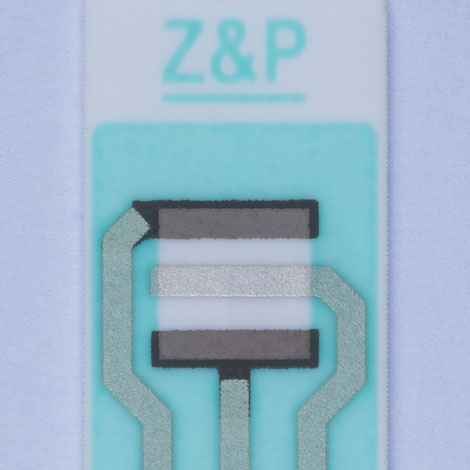
WAFER AND BATCH MAPPING.
Zimmer and Peacock has a database in place which allows us to map out the entire production process and link an electrode's position within manufacturing to the electrode's functional performance. In effect we give each electrode within a manufacturing batch a unique identifier number (UIN) and we are then able to track that individual electrode through manufacturing to functional testing.
The principle is that if you are controlling inputs to a manufactured product then the product output will be a function of how well you control the inputs, but there are parameters that can be overlooked and are not kept constant for all electrodes within a batch of electrodes, and these are time and position within the manufacturing run. At ZP we are unique in the contract electrode, biosensor and medical diagnostic world as we are sampling and functionally testing electrodes and are able to link sensor/electrode function to the electrodes position and time of manufacturing. We are able to do this in parallel manner as to get high numbers for statistical analysis.